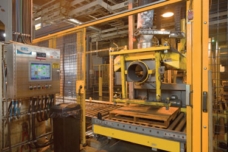
Oprima para ampliar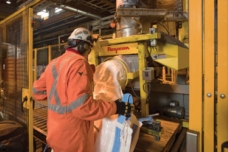
Oprima para ampliarCada llenador de supersacos presenta un cabezal articulado de llenado, abatible hacia abajo, que permite al operador acceder de manera segura a todos los puntos de conexión del supersaco desde el nivel del piso. Las celdas de carga miden el aumento de peso del saco, lo que permite que un PLC deje de llenar el saco una vez que alcanza el peso establecido.
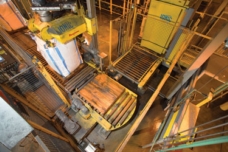
Oprima para ampliar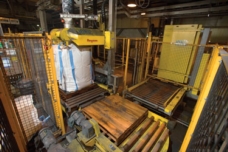
Oprima para ampliarEl dispensador automático de paletas (derecha) alimenta paletas a la llenadora de supersacos que recibe gránulos de concentrado de cobre desde la tolva de arriba de 10 m.t. de capacidad
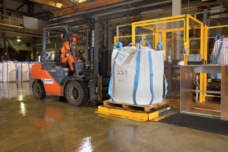
Oprima para ampliar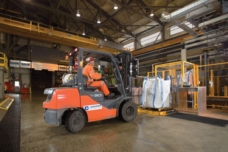
Oprima para ampliar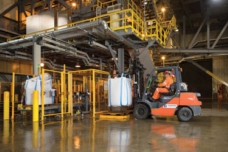
Oprima para ampliarEl supersaco lleno se retira del compartimiento de retención al final del transportador de rodillos de 7,5 m de largo.
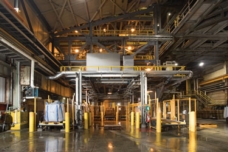
Oprima para ampliar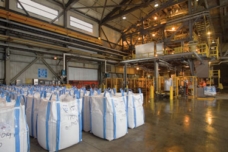
Oprima para ampliarEl sistema automatizado de llenado de supersacos incluye dos llenadores de supersacos (atras), un dispensador de paletas central y dos transportadores de rodillos de 7,5 m de largo desde los cuales una montacargas de horquillas toma los sacos llenos para su despacho.
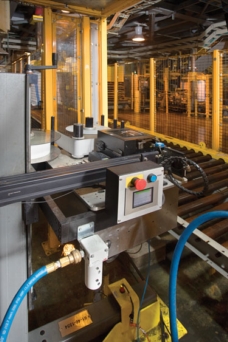
Oprima para ampliarLos sistemas de dispensación de paletas y llenado de supersacos están equipados con controles automáticos, sistemas de seguridad y protectores.